effect of high manganese sinter in blast furnace
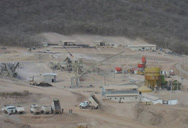
Experience of Using Manganese-Containing Materials in Blast-Furnace ...
2020.1.21 The paper discusses the experience gathered at the Yenakievo metallurgical plant and Dnepr metallurgical complex with respect to using manganese-containing materials in the blast-furnace charge, which results in one of the greatest
More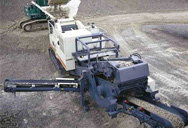
Making Blast-Furnace Ferromanganese with the Use of
2017.8.25 In the trial blast-furnace heats conducted to make ferromanganese,high-basicity manganese sinter was added to the charge in the amount 41% for a period of 27
More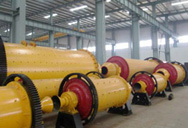
Effect of Oxides of Magnesium and Manganese and the
2016.3.28 It was established by laboratory studies and confirmed by factory tests that the filterability of molten blast-furnace slag is affected by the presence of the oxides
More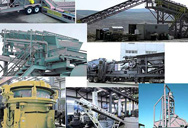
A Review of the Production of Ferromanganese
2011.5.6 Today's main share of the worldwide high-carbon ferromanganese (HCFeMn) production is realized in submerged arc
More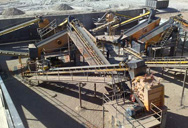
Evaluation of Sinter Quality for Improvement in Gas
High RDI sinter deteriorates gas permeability in the upper part of the blast furnace because the particle size of the sinter is easily reduced by reduction degradation (powdering) in
More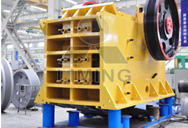
A Review of the Production of Ferromanganese in Blast
The production of high-carbon ferromanganese in blast furnaces is reviewed, based on public literature and requests to consultants and suppliers to the industry.
More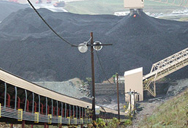
Properties of blast-furnace slags containing high amounts of manganese ...
1999.2.1 A study was undertaken to assess the properties of five ground granulated blast-furnace slags produced by the ferroalloy industry. These slags are characterized by
More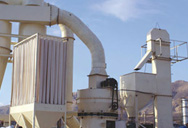
Sintering - Springer
2020.8.18 sinter degradation in the blast furnace during the reduction in the low-temperature zone; reducibility test, as it gives a measure of the ability of the sintered
More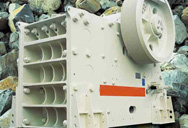
Assessment of blast furnace behaviour through
2024.1.8 The increased fuel rate in sintermaking causes an increase in FeO content of sinter. The present paper discusses the effect of high FeO and lowering MgO in sinter
More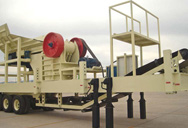
Charge material distribution behaviour in blast furnace charging system ...
2020.4.15 This research paper presents discrete element modelling (DEM) study to investigate, characterise and compare the effects of initial positioning of high flowability
More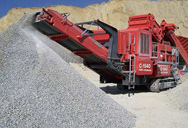
Investigating the Effect of the Iron Ore Pellet Addition on the ...
2024.1.8 The efficient operation of a blast furnace requires burden materials with high softening temperatures and a narrow softening–melting range. This leads to the formation of a thinner cohesive zone in the lower part of the furnace, which improves permeability. In this study, softening–melting tests were conducted on pellets with different levels of basicity,
More
Blast Furnace Productivity and the Influencing
2013.6.23 Sinter is to have optimum grain distribution, high strength, high reducibility, high porosity, softening temperatures greater than 1250 deg C, constant FeO content in the range of 7 % to 8 % and constant
More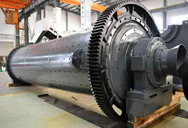
Effect of Mixed Charging of Nut Coke and Sinter on
In this paper, the effect of mixed charging of nut coke and sinter on reduction and softening-melting properties in the hydrogen-rich smelting process of blast furnace is studied. The results showed that the close contact between nut coke and sinter promoted carbon dissolution and water–gas reaction to generate more CO and H2, thus increasing ...
More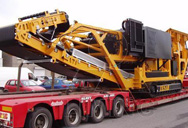
Review of hydrogen-rich ironmaking technology in blast furnace
The global warming promotes the steel industry to replace part of coke by injecting hydrogen-rich fuel into the blast furnace to reduce CO2 emissions and energy consumption. In this paper, the injected hydrogen-rich fuels and effects of hydrogen-rich smelting on burden reduction and property evolution were introduced, and the hot events related to
More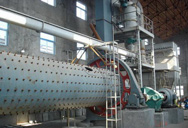
Investigating the Effect of the Iron Ore Pellet Addition
2024.1.11 content compared to iron ore or sinter, making them suitable for blast furnace feed. In the blast furnace, a combination of different iron-bearing materials (IBM) is charged since no single IBM can meet the required slag chemistry.3,4 By dissect-ing a chilled furnace,5,6 it has been observed that the furnace consists of a granular zone
More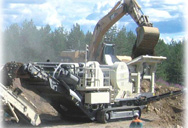
Effect of FeO concentration in sinter iron ore on
2022.10.1 Request PDF Effect of FeO concentration in sinter iron ore on reduction behavior in a hydrogen-enriched blast furnace Japan started the national project “COURSE 50” for CO2 reduction in ...
More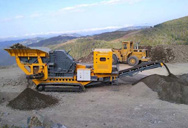
Behavior of chromium in the reduction and smelting of high
2023.1.1 The smelting experiments were carried out in a high-temperature electric furnace. Fig. 1 shows the schematic diagram of the experimental process. The raw materials used in the study included nickel laterite sinters, iron ores, coke, CaCO 3, and SiO 2.The nickel laterite sinters, iron ores, and coke were dried in a drying oven at 110 °C for 3 h to
More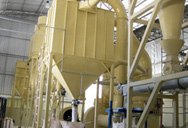
Impact of Sinter Basicity and Alumina on Softening Melting
2019.11.26 Softening–melting (SM) experiments have been carried out by using sinter basicity (CaO/SiO2) 1.74 to 2.09 and alumina content 2.90 to 3.39%. The objective of the work is to find the relation between sinter basicity and alumina on SM temperature range, so that we can improve the furnace performance. The increase in basicity of sinter
More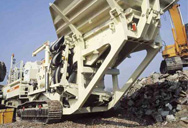
Effect of Nut Coke-sinter Mixture on the Blast Furnace Performance
2011.3.18 In meantime modern blast furnaces use nut coke with different amount (10–140 kg/t hot metal) and different grain size (10–40 mm) in the sinter layer to reduce the coke losses. The objective of ...
More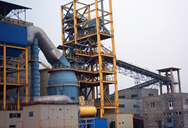
effect of high manganese sinter in blast furnace
The high permeability of the sinter allows an increased blast volume and thus an increased productivity of the blast furnaces, leading to lower specific thermal losses. The high reducibility reduces the fixed carbon consumption. Both effects have been taken into account in a blast furnace model developed by ERAMET Research Center.
More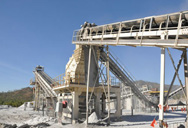
Influence of sinter basicity (CaO/SiO2) on low and high
2014.4.11 Abstract. Iron ore sinter, constituting a major proportion of blast furnace burden, significantly impacts the blast furnace performance. The chemical composition of iron ore fines, particularly alumina, sinter basicity and sinter MgO together with the thermal conditions that sinter blends are subjected to play an important role in the formation of
More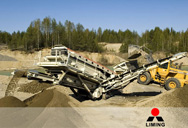
Effect of Nut Coke-sinter Mixture on the Blast Furnace
In meantime modern blast furnaces use nut coke with different amount (10–140kg/t hot metal) and differ-ent grain size (10–40mm) in the sinter layer to reduce the coke losses. The objective of this paper is to clar-ify the influence of nut coke on the shaft permeability and sinter reducibility under blast furnace simulating conditions.
More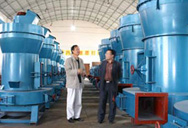
Study on Sintering Technology of Manganese Ore Fines
2024.6.20 The experimentation allowing comparison of manganese ore fines pellet sintering and traditional sintering of manganese ore fines in terms of sintering performance are studied. The results show that, compared with traditional sintering, the pellet-sintering process can significantly reduce the coke level while ensuring the quality of sinter. Pellet
More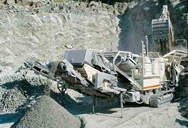
What are the advantages and disadvantages of high silica in
ArcelorMittal South Africa. High silica, low alumina iron ores have no specific disadvantage in blast furnace iron making, unless silica is so high that it results in large slag volume. Low Al2O3 ...
More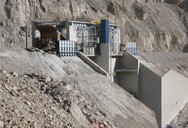
Optimisation of MgO addition in low and high silica iron ore sinter
2013.12.6 A recent trend in blast furnace operation shows that there is a considerable increase in usage of dolomite as a basic flux either directly or through sinter. Recently the silica levels in the sinter product of Sinter plant 1(SP1) of JSW Steel Limited have been fluctuating in the range of 55–96% due to variation in silica content of iron ...
More
Magnesium-containing pellet regulating blast furnace
2024.5.26 MgO participates in all stages of sintering, pelletizing, and blast furnace ironmaking, and synergistically optimizing the distribution of MgO in ferrous burden can effectively enhance the interaction within the ferrous burdens and optimize the softening–melting properties of the mixed burden. Magnesium-containing pellets mixed
More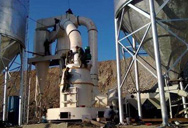
Fundamental mechanism of effects of MgO on sinter strength
2019.11.6 MgO-containing flux may have a series of effects on the quality of sinter and performances of the blast furnace. Thus, the fundamental mechanism of the effects of MgO on the sinter strength was investigated. Both the chemical reagent and industrial flux were used for preparing the specimens. The experimental results show that the sinter
More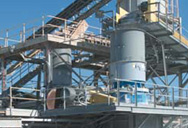
Effectiveness of Using High Gas Pressure in a Blast Furnace
2015.12.8 This article refutes theoretical arguments that it is inexpedient to increase gas pressure in a blast furnace as a means of intensifying the smelting operation. The intensifying effect of higher gas pressure has been proven by the results obtained on three blast furnaces at the Novolipetsk Metallurgical Combine. The productivity of these
More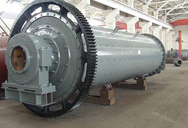
Blast furnace ironmaking and its ferrous burden quality
2022.1.1 The integrated iron and steelmaking route involves blast furnace (BF) ironmaking followed by basic oxygen furnace (BOF) steelmaking. The BF uses sinter, pellets, and lump ore as iron-bearing raw materials, and coke and pulverized coal as fuel and reducing agents to produce hot metal with consistent quality for the BOF process.
More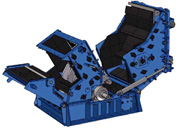
Improved iron-ore sinter for blast furnaces Steel in Translation
2015.7.26 Abstract. Technology has been developed for the production of fluxed local sinter and pellets with residual carbon for blast-furnace use. The new products have better metallurgical characteristics than existing materials.
More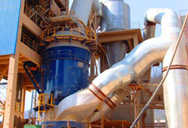
A Review of the Production of Ferromanganese in Blast Furnace
Production of ferromanganese in blast furnaces High C FeMn world production has been in the order of the 5 Mtpy in the first decade of this century. In 2008, 4.795.100 t has been produced, of which 3.419.900 t in Asia [1]. China is the largest producer, making half of the world’s production.
More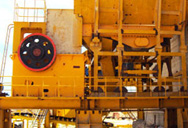
Effect of Nut Coke-sinter Mixture on the Blast Furnace
2011.3.6 In meantime modern blast furnaces use nut coke with different amount (10–140 kg/t hot metal) and different grain size (10–40 mm) in the sinter layer to reduce the coke losses. The objective of ...
More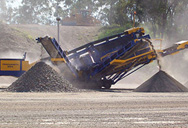
Effect of Oxides of Magnesium and Manganese and the
2016.3.28 It was established by laboratory studies and confirmed by factory tests that the filterability of molten blast-furnace slag is affected by the presence of the oxides MgO, MnO, and CaO, which are added to charge that is used to make sinter. The magnitude of this effect depends on the composition of the minerals that contain these oxides.
More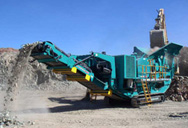
Effect of Nut Coke-sinter Mixture on the Blast Furnace
Among different ways to reduce the coke consumption in the blast furnace, not so much attention was paid for decreasing the coke losses through finding suitable application of small size coke called “nut coke”. In meantime modern blast furnaces use nut coke with different amount (10–140 kg/t hot metal) and different grain size (10–40 mm) in the sinter
More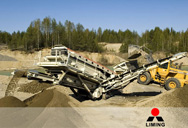
Effect of Nut Coke-sinter Mixture on the Blast Furnace
In meantime modern blast furnaces use nut coke with different amount (10–140kg/t hot metal) and differ-ent grain size (10–40mm) in the sinter layer to reduce the coke losses. The objective of this paper is to clar-ify the influence of nut coke on the shaft permeability and sinter reducibility under blast furnace simulating conditions.
More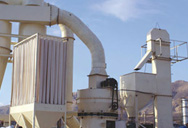
The Sintering Process of Iron Ore Fines – IspatGuru
The process of sintering is basically a pre-treatment process step during iron making for the production of the charge material called sinter for the blast furnace from iron ore fines and also from metallurgical wastes (collected dusts, sludge and mill scale etc.). The sintering technology was originally developed for the purpose of utilizing ...
More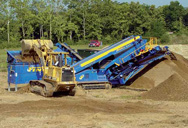
Measures of Decreasing Blast Furnace Fuel Consumption and
2008.9.1 However, in view of blast furnace operation, MgO is used to enhance the thermal stability, viscosity, and fluidity of slag when the Al20;i content increases because of the addition of imported ores. Thus, reasonable MgO content must be determined by the composition of slag systems for blast furnace, to avoid negative effect on sinter caused
More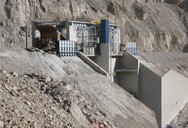
Charge material distribution behaviour in blast furnace
2020.2.1 Bed permeability is a crucial factor in blast furnace performance which depends on the material distribution achieved through charging. Since a homogeneous bed of pellet and sinter is recommended ...
More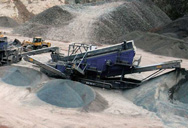
FactSage Studies to Identify the Optimum Slag Regime for Blast Furnace ...
2020.11.29 On increasing the MgO concentration beyond a value of 14%, the liquidus temperature of the slag system increases. The Blast furnace (BF) can be operated with 22% Al 2 O 3 slag without the use of ...
More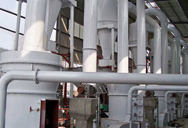
Slag and its Role in Blast Furnace Ironmaking – IspatGuru
2015.8.7 High Al2O3 slag is encountered mainly with Indian blast furnaces because of high Al2O3/SiO2 ratio in the iron ore as well as in the sinter and high ash content in the coke. These slags are having high viscosities. The viscosity of liquid slag is determined primarily by its temperature and the chemical composition.
MoreArticle aléatoire
- coût de concasseur milieu mou arabie saoudite
- sable faisant la machine de la chine
- frais de concassage de calcaire
- comment ne agrégats produisent de l usine de concassage
- charbon marteau prix dl'usine
- Machoires Primaire Afrique concasseur de Serie De Pe Mobiles
- Agrégat de construction concasseur à còne en ac usé à vendre
- concasseur à machoires calcaire inde
- moulins à rouleaux fournisseurs
- Concasseur à mâchoires Fabricant En Afrique du Sud
- concasseur charbon de puissance
- broyeur de fruits pour confiture
- utilise des fraiseuse universelle
- la construction de transport et équipements miniers vietnam
- concasseur petite échelle Indonésie vendre en arménie
- cout de 60 mm de pierre concassee au Gujarat
- broyage calendrier de maintenance de usine
- les etapes de charbon
- franchise opportunities in clay brick manufacturing
- Concasseur Peringkat Daya
- broyeur concasseur
- chancadora de cono y mandibula
- pouzzolane 200 tph broyeur 3 étapes
- équipement d'extraction d'argile de kaolin de carrières
- Prix unité de moulin broyage de ciment au Niger
- deux rouleau de papier de capacite de l'usine l'impact
- inde concasseurs à cône portable
- des broyeurs Indonésie boulets
- equipements de mines burkina faso
- Pierre De Basalte De Resistance A La Compression