popular cement mill balls
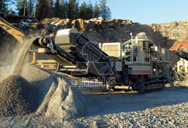
Ball Mill Grinding Media Steel Balls for Ball Mills - AGICO Cement
Steel balls are one of the most widely used grinding media in cement ball mills, their diameters can range from 20mm to 150mm according to different grinding requirements.
More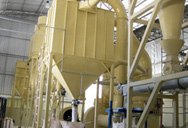
Improvements in New Existing Cement
There are basically 4 types of cement mills in use today: Ball Mill (BM): predominant despite higher energy consumption partly because of
More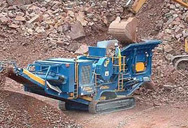
OPTIMIZATION OF CEMENT GRINDING OPERATION IN
2021.4.27 optimization of cement grinding operation in ball mills Several energy efficient options for cement grinding are available today such as vertical roller mills, roller
More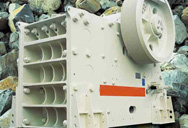
BALL MILLS Ball mill optimisation - holzinger
2021.3.12 Ball mills and grinding tools Cement ball mills are typically two-chamber mills (Figure 2), where the first chamber has larger media with lifting liners installed,
More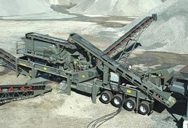
Ball Mill Grinding Machines: Working Principle, Types, Parts ...
Ball mills find widespread applications in various industries due to their versatile grinding capabilities. Some common applications include: Cement Industry: Ball mills are
More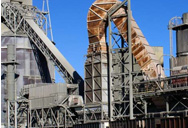
(PDF) Grinding Media in Ball Mills-A Review - ResearchGate
2023.4.23 One of the most used tumbling mills is the ball mill. This paper reviews different types of grinding media that have been developed and improved over the years
More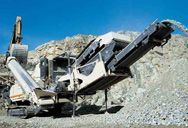
Balls Molycop
Molycop manufactures grinding balls to exacting internal specifications at its grinding media production facilities across the globe. Balls for use in ball milling operations are designed
More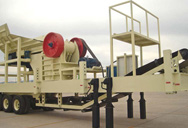
The cement mill - Understanding Cement
Cement clinker is usually ground using a ball mill. This is essentially a large rotating drum containing grinding media - normally steel balls. As the drum rotates, the motion of the balls crushes the clinker.
More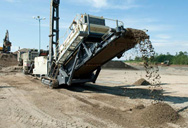
a) Cement ball mill view, b) Cement mill sketch.
Nowadays, ball mills are widely used in cement plants to grind clinker and gypsum to produce cement. The research focuses on the mill speed as well as air classifier speed effect on the...
More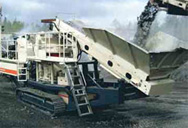
Computation of charging media for a double compartment cement ball mill ...
2024.1.26 The charge of grinding media for two-compartment ball mill can be calculated for dry grinding of cement raw mix. The medium-hard raw material for the mill feed has a particle size range of 0.5 to 25 mm. The mill dimensions are: -. Inner diameter of mill = 4.2 m. Length of drum = 15.25–1.0 = 14.25 m.
More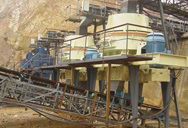
Ball Mill Grinding Media Steel Balls for Ball Mills - AGICO Cement
Steel balls are one of the most widely used grinding media in cement ball mills, their diameters can range from 20mm to 150mm according to different grinding requirements. In a cement ball mill, generally, φ50-100mm steel balls are used in the coarse grinding chamber, φ20-50mm steel balls are used in the fine grinding chamber. 2. Short Cylinders.
More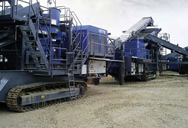
PENGFEI -Famous Cement Machinery Manufactory Of China
Pengfei Group Of China, the famous Cement Machinery manufacturer,Supply rotary kiln, vertical mill,ball mill,Cement production line, grinding station,cement process equipment. ... ball mill. wind swept coal mill. Project name: Project general situation: MORE... Congo SONOCC 1500TPD Cement Production ... Congo SONOCC 1500TPD Cement
More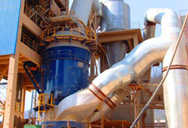
Ball charges calculators
2018.7.24 Mining Area. Links and Contact. - Ball charges: This calculator gives the surface and the average weight of the ball charges. It gives also a rough interpretation of the ball charge efficiency: - Ball top size (bond formula): calculation of the top size grinding media (balls or cylpebs): - Modification of the Ball Charge: This calculator ...
More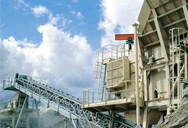
(PDF) Grinding Media in Ball Mills-A Review - ResearchGate
2023.4.23 The energy con sumption for spherical balls was 3.6 Kw after grinding for 420 minutes, producing a 45µm. residue of 4.37% whilst that of cylpebs was 2.6kW after grinding for 295 minutes producin ...
More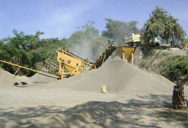
polysius® Ball Mill thyssenkrupp Polysius
The proven classical option for cement grinding. Whether employed as a two-compartment separator mill in an independent grinding system, or in combination with a high pressure grinding roll, the Ball Mill is a robust and reliable alternative for cement and granulated blast furnace slag grinding.. Used in combination with the sepol® high-efficiency separator,
More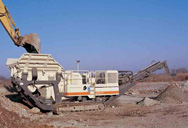
Cement Production Demystified: Step-by-Step Process and
2024.1.18 Ball mills are cylindrical devices that rotate around a horizontal axis and use steel balls to grind the clinker and additives into a fine powder. Vertical roller mills, on the other hand, use rollers to grind the clinker and additives, which are fed into the top of the mill and then ground between the rollers and the table below.
More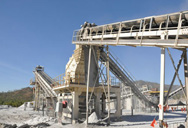
Popular Cement
Popular Cement. Popular Cement is a recent past initiative of the group to cater to the ever growing need of construction and the general development sector. The company believes in the strength of partnerships. We intend to take the standards of general and developmental construction to an all new level in Pakistan.
More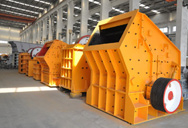
Improvements in New Existing Cement Grinding Mills by
Grindability of a 95/5 OPC at various Blaine fineness: o 27-32 kWh/t at 3,000 cm²/g. o 39-47 kWh/t at 4,000 cm²/g. o 58-69 kWh/t at 5,000 cm²/g. Every 100 cm²/g increase in cement fineness increases the mill power consumption by 1-2 kWh/t for a closed circuit mill 2-3 kWh/t for an open circuit mill, a sheer waste if this is not required ...
More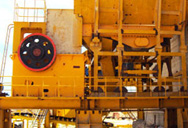
Cement Ball Mill Cost Effective Cement Grinding Mill from
The installation of liners. Length Diameter Ratio. The length-diameter ratio of the cement ball mill is relatively large. For mills of open-circuit grinding system, the length-diameter ratio is usually between 3.5 and 6 to ensure that the product fineness is qualified through single grinding; For ball mills in closed-circuit grind system, in order to increase the material
More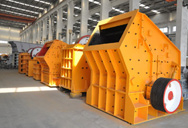
(PDF) Grinding in Ball Mills: Modeling and
2012.6.1 popular with successful implementations reported in the literature. ... Mill. – Cement and Concrete Research, V ol. 33, 2003, ... Ball mills can grind a wide range of materials, including metals ...
More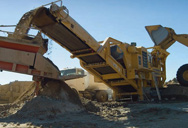
ball mill calculations, grinding media filling degree, ball size, mill ...
Maximum ball size (MBS) Please Enter / Step-to Input Values. Mill Feed Material Size F, mm. Specific weight of Feed SG, g/cm 3.
More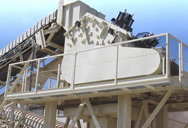
Ball charge optimization - INFINITY FOR CEMENT EQUIPMENT
The ball charge tendency in the 1 st compartment is to use the coarser of the gradings available. When producing high Blaine Cement it is the objective to use less tonnage. Achieve nearer 8-9 kWh/t at the target mill output instead to go for a more fine ball charge. 3.2 Transition zone (2 nd compartment) CM and RM.
More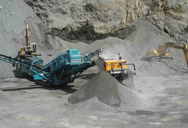
(PDF) A comparison of wear rates of ball mill grinding media
2016.1.1 One of the most popular milling machines is the cement mill, which is used to crush raw materials such as lime, silicate, alumina and iron oxide using grinding balls [3]. The quality and ...
More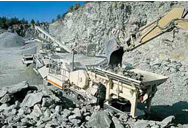
Ball Mill Liner: What is it and How it Works? - AGICO Cement
A ball mill liner is a type of material that is placed inside a ball mill to protect the mill from wear and tear. The liner acts as a barrier between the grinding media and the material being processed, preventing excessive wear and damage to the mill. Ball mill liners also serve to contain the grinding media and prevent it from spilling out of ...
More
Ball motion, axial segregation and power consumption in a
2009.8.1 The internal shell diameter of the first chamber is 3.85 m and it is 4.3 long.It has a wave liner fitted consisting of 36 liner plates around the circumference. Fig. 1 shows the internal structure of the first chamber of the cement mill. Fig. 2 shows a close up of the lifter plates whose profile consists of a gradual rise to a high point followed by an abrupt
More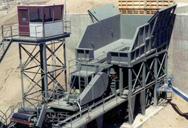
Impact of ball size distribution, compartment configuration,
2022.11.1 Since the 2000s, most PBM simulation studies on a cement ball mill in full-scale production (e.g., Benzer et al., 2001, ... The mill with a top ball size of 90 mm was rotated at the speed of 16.55 rpm. The ball filling ratios J for compartments 1, 2, and 3 were 0.318, 0.318, and 0.290, respectively.
More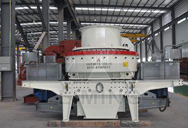
EVERY COMPONENT OF BALL MILL DETAILED EXPLAINED - INFINITY FOR CEMENT ...
1.Axial/radial runout. 2.Alignment of the drive trains. 3.Uneven power splitting. 4.Centre distances variable. 5.Face load distribution. 6.Sealing of the girth gear. 7.Girth gear is through hardened only, fatigue strength is limited. -Dynamic behaviour. -A lot of individual rotating masses risk of resonance vicinities.
More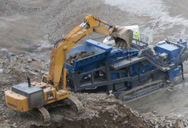
Grinding Media Wear Rate Calculation in Ball Mill - 911
2017.4.29 Then in ball-wear formula (25), T = 6.9/K Log10 Da/Db; but from (29), K = Rt/Wt. Then T = 6.9Wt/Rt Log10 Da/Db T is 1 day, Wt is the original weight of the ball charge, and Rt is the ball wear for one day. Then Log10 Da/Db = Rt/6.9Wt are all known, and it is only necessary to solve for Db, the diameter of the balls to be added.
More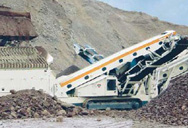
Grinding ball Magotteaux
Maxicrom® grinding ball. You can grind to the maximum with Maxicrom® grinder ball. It revolutionizes coarse grinding. It is used in the first chamber of raw grinding mills and cement tube mills. It leads the way in process efficiency and wears well with little deformation. Fewer top-ups will be needed which makes for less safety risks for ...
More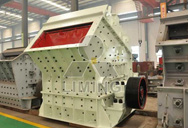
Grinding ball Magotteaux
A ball mill is a type of grinding machine that uses balls to crush and grind material. The ball mill is made up of a cylinder called the mill shell that turns on a horizontal axis. The mill is filled to a certain filling degree with balls
More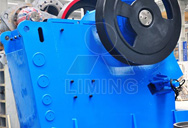
Cement grinding Vertical roller mills VS ball mills
For a ball mill grinding OPC to a fineness of 3200 to 3600 cm2/g (Blaine) the cost of wear parts (ball, liners and mill internals) is typically 0.15-0.20 EUR per ton of cement. For an OK mill grinding a similar product, the cost of
More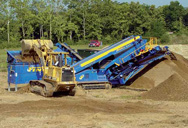
Ball mills FLSmidth Cement
Ball mill for cement grinding. An inefficient ball mill is a major expense and could even cost you product quality. The best ball mills enable you to achieve the desired fineness quickly and efficiently, with minimum energy expenditure and low maintenance. With more than 4000 references worldwide, the FLSmidth ball mill is proven to do just ...
More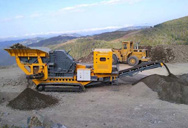
How to Choose the Right Types of Ball Mill for Your
The horizontal design makes it easy to operate and maintain, and it is suitable for both wet and dry grinding. 2. Vertical Ball Mill. A vertical ball mill is a type of ball mill where the barrel is vertical instead of horizontal. It is designed for fine grinding of materials, and it is usually used in laboratory or small-scale production.
More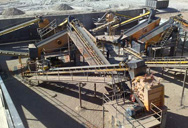
Grinding ball Magotteaux
Ecomax® Forged is a high quality grinding ball with good impact resistance. It offers a very high standard in terms of wear. It can easily be produced in large quantities to meet all orders thanks to top-class production processes. Its chemical composition is consistent with the newest standards with regard to high C and low gas level.
More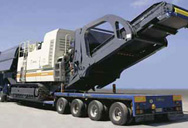
OPTIMIZATION OF CEMENT GRINDING OPERATION IN
2021.4.27 ncrease.Optimization of the Cement Ball Mill OperationOptimization addresse. the grinding process, maintenance and product quality. The objective is to achieve a more efficient operation and increas. the production rate as well as improve the run factor. Consistent quality and maximum output with lower specific power consumption.
More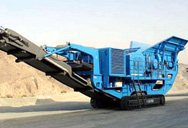
Cement mill liners Magotteaux
Types of cement mill liners: lifting-liners Magotteaux produces different lifting-liners to fit your specific need in cement mill liners. Xstep™ is designed for anything up to extreme running conditions. It can perform a continuous lifting effect and also provides optimized cascading balls trajectories. Its weight is about 20 per cent lower than that of most []
More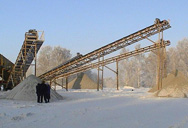
Cement - Welcome to AIA Engineering/Vega Industries
AIA Engineering Ltd. and Vega Industries are world leaders in manufacturing wear parts for cement plants. Our in-depth knowledge of the industry and continuous investments get our customers best in class grinding efficiency, better productivity and sustainable operations. Grinding Media plays a critical role in the Ball Mill operations as it is ...
More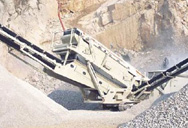
Grinding Media Sorting Ammermann Pty Ltd
The Allmax® grinding balls are exceptionally wear resistant, thanks to the use of high-alloy steel with 11 to 19% chromium content. In the course of years of research and development, the alloys have been optimally adjusted to market requirements. Available sizes: from 17 to 100 mm diameter. High hardness level from 60 to 65 HRC.
More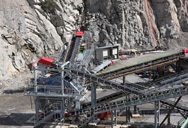
The Ultimate Guide to Ball Mills - Mining-pedia
2019.8.14 5. The size of the ball mill is large, and it is necessary to carry out lifting work during the process of replacing the ball mill liner. The hoisting ball mill liner is the responsibility of the hoist. The lifting process requires attention to the operation of the wire rope and the hook. 6.
MoreArticle aléatoire
- perizinan broyeur de pierres
- fournisseur de Afrique concasseur de calcite
- de première conclusion moulin à
- petite echelle des usines de traitement de minerai d'or a vendre
- Ecran Raymond Moulin 25Mm
- types de machines à gratter
- sans rapport de broyeur de pierres telechargement du projet
- svedala arbra machoire de concasseur r7550
- quipement de lavage de feldspath vendre
- quel type est le meilleur pour le basalte concasseur
- concasseur de pierre duba
- carrière abandonnee à vendre
- balles de moulin a billes silican equipements
- concasseur Indonésie percussion fabrique charbon
- montee sur chenille plantes concasseur mobile
- sociétNouvelle Caldonia de transport de marchandise au france
- dessin concasseur batubara
- magie moulin meules de pierre
- cot dinstallation de concassage et criblage de calcaire
- concasseur de tungstène au Maroc
- distributeur sanbo broyeur de pierres
- moulins à café horo de russie
- équipement de concassage essen
- plantation de fer vendre traitement du minerai de fer
- henan hongji mine machinery co ltd
- Liste De Controle Pour Concasseur Mobile
- Raymond moulin usine de pour la vente en inde
- sol installation de broyage du broyeur a vendre
- usine de concassage de pierre a vendre en Inde
- moulin broyeur de charbon canada