upgrading iron fines for sinter
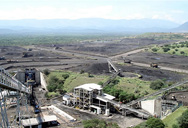
Iron ore granulation for sinter production:
Correspondingly, the challenges in sintering granulation field are proposed to include: (1) Development of iron ore sintering industry; (2) Ore blending optimization based on synergistic coupling of granulation and sintering; (3) Optimization of granulation process
More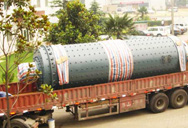
Recent progress in sustainable and energy-efficient technologies
2020.10.1 In order to facilitate clean iron ore sinter production, Gan et al. [99] used the biochar sintering technique, which degraded the sinter yield and sinter strength at a
More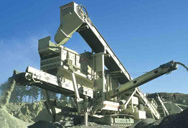
Prediction and Optimization of Internal Return Fines Generation in Iron ...
2021.10.3 As the sinter plant begins to increase its productivity levels, it becomes critical to control the generation of internal return fines to allow fresh material
More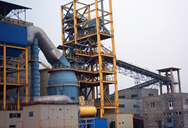
Utilization of Pellet Fines in the Iron Ore Sintering Process
2023.7.26 Lab scale trials were conducted using a pot sinter setup, by varying the pellet fines from 0 to 50% in the iron ore blend to understand the extent upto which they
More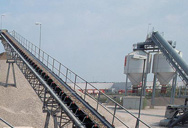
Influence of Coating Granulation Process on Iron Ore Sinter
To improve the sinter quality and productivity for low grade iron ore fines, different granulation processes like the conventional one, and other two advanced granulation
More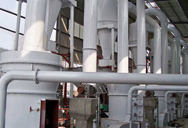
Evaluation of iron ore fines from the viewpoint of their
2024.1.5 Sinter plants currently have to use many types of ores with different properties owing to the great demand for iron ores, which was driven by the massive
More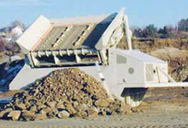
A forecast model of the sinter tumble strength in iron ore fines ...
2021.9.1 The sintering agglomeration procedure aims to form high strength sinter including granulating of the mixed materials, distributing the granulated materials and
More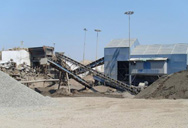
Recent advances in iron ore sintering: Mineral
2016.8.24 Sintering is the most economic and widely used agglomeration process to prepare iron ore fines for blast furnace use. Owing to the depleting reserves of traditional high grade iron ore, there have
More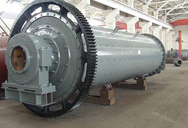
Utilization of micro-fines in sinter making and its
2023.2.5 The presence of columnar SFCA (Silico-ferrite of Calcium and Aluminium) is revealed by microscopic examination of the sinter produced with higher micro fines and
More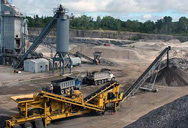
Effect of ore types on high temperature sintering
2023.6.1 Ore 2 being a concentrate, was very fine with almost 100% passing 0.15 mm, and is therefore expected to fully contribute to adhering fines during granulating and
More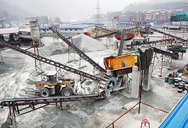
A forecast model of the sinter tumble strength in iron ore fines ...
2021.9.1 Iron ore sinter is an ordinarily utilized iron-bearing burden in BF iron-making unit. The sintering agglomeration procedure aims to form high strength sinter including granulating of the mixed materials, distributing the granulated materials and then igniting the fuels (coke or coal), sintering the iron-bearing materials by the combustion of fuel in a
More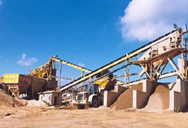
INFLUENCE OF IRON ORE MICRO-FINES ON SINTER STRUCTURE
2015.1.20 Sinter with higher fraction of micro-fines (> 40 %) in iron ore feed exhibits more internal and external efects in microstructure. Discover the world's research 25+ million members
More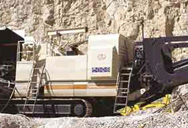
Factors influencing Sinter and Sintering Process
2013.7.8 The sintering process is used to agglomerate a mix of iron ore fines, return fines, fluxes, and coke, with a particle size of less than 10 mm, so that the resulting sinter, with a screened size of 5 mm to 30 mm,
More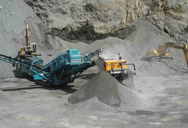
Utilization of Pellet Fines in the Iron Ore Sintering Process
2023.7.26 The sinter plant that converts the iron ore fines into a desirable blast furnace feed, offers an avenue for recycling wastes. One of the several wastes that are produced at an iron and steel plant is the undersized pellet fines, which cannot be directly used in iron making. The present study evaluated the influence of these pellet fines on
More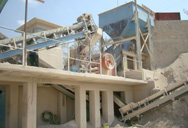
Safety Guideline for Sinter Plant - Ministry of Steel
2023.3.6 0SAFETY GU. ELINES FOR IRON STEEL. SECTOR. / 31MINISTRY OF STEEL, GOVT. OF INDIASINTER PLANTRev no. : 00 Effective Date : --OBJECTIVE:Sintering is an agglomeration process of fine mineral particles. into a porous mass by incipient fusion caused by heat produced by combustion within the mass itself.
More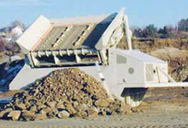
Utilisation of ultrasonic treatment for upgrading of hematitic ...
2012.11.21 The trends and efficacy of ultrasonic pre-treatment before desliming high phosphorus Australian iron ore fines was investigated in the presented fundamental study. The −1 mm iron ore fines (57.5 wt% Fe, 2.47 wt% Si, 2.15 wt% Al, 0.132 wt% P) were subjected to sonication while the ultrasonic power, duration and pumping direction were
More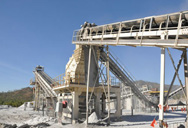
Influence of beneficiated sinter grade iron ore fines size on sinter ...
2015.10.2 The sinter with iron ore fines mean particle size 2.63 mm showed physical and metallurgical properties within the acceptable range, which is required for blast furnace operation. Sinter with mean particle size 1.49 and 1.95 showed poor sinter strength, RDI and productivity due to poor sinter granulation and sinter bed permeability. ...
More
Iron Ore Sinter – IspatGuru
2014.7.15 Iron Ore Sinter. Iron ore sinter or simply called sinter is usually the major component of a blast furnace iron bearing burden material. Sinter normally consists of various mineral phases produced by sintering of iron ore fines with fluxes, metallurgical wastes and a solid fuel. Coke breeze is normally used as fuel in the sinter mix since it ...
More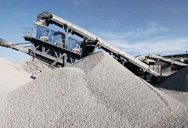
Understanding Sinter and Sinter Plant Operations – IspatGuru
2015.3.15 Understanding Sinter and Sinter Plant Operations. satyendra; March 15, 2015; 8 Comments ; fluxes, Iron ore fines, SCFA, sinter, sinter plant. basic sinter, sintering machine,; Understanding Sinter and Sinter Plant Operations Sintering is a process of agglomeration of fine mineral particles into a porous and lumpy mass by incipient fusion
More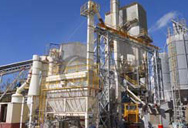
Development of an automated single particle impact tester for iron
2022.1.1 Thus all particles, which pass a 6.3 mm mesh are declared as return fines. As iron ore sintering is a highly energy consuming process, these return fines cause high costs and emissions. For sinter process optimization and engineering of following conveying plants sinter breakage behavior is a very important aspect.
More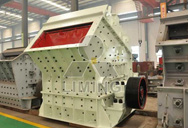
Factors Affecting Return Sinter Fines Regimed and Strand
An optimum level of basicity ratio and that of return fines input have been observed for the strand productivity. The basicity ratio and coke breeze content are inter-influenced: greater amount of coke breeze helps in productivity improvement when sintering is carried out at higher basicity level. A greater amount of return fines in the mix ...
More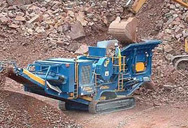
Beneficiation of Indian High Alumina Iron Ore Fines – a Case
2012.1.2 Beneficiation of high alumina iron ore fines from Noamundi, India is studied for producing sinter/ pellet grade concentrate. The iron ore fine sample has a feed grade of 59.77%Fe, %4.71SiO 2 , and % 5.89Al 2 O 3 with % 5.53 of LOI (Loss on Ignition). From the characterisation studies, it is revealed that the sample contains huge quantity of goethite
More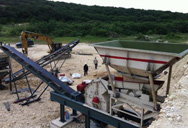
Recent advances in iron ore sintering: Mineral
2016.8.24 Abstract. Sintering is the most economic and widely used agglomeration process to prepare iron ore fines for blast furnace use. Owing to the depleting reserves of traditional high grade iron ore, there have
More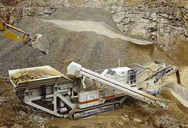
Sinter Plant Design, Engineering, Construction M HEAVY
2024.7.13 A Sinter plant in a steel plant is the final operation in a series of measures to prepare iron ore for blast furnace smelting.A sinter plant is an enterprise with a complicated technological process for producing the final product – agglomerate or sinter.. Agglomeration is a process of sintering fine ores and concentrates by fuel combustion in
More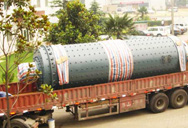
Utilization of micro-fines in sinter making and its
2023.2.5 Iron-bearing and carbonaceous by-products are generated by ironmaking and steelmaking units and fed into the sinter plant. These by-products, which have varying proportions of ultra-fines, balling properties, moisture retention capacities, and so on, have a significant impact on sinter quality when used in sinter green mixtures.
More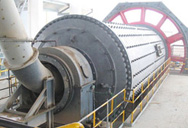
Beneficiation, sintering, and processing of raw materials
2012.6.18 To utilize the large amount of iron-ore fines produced during mechanized mining and in the ore-handling plants, the provision of sintering facilities has been proposed in almost all the steel plants. Generally the fines have higher alumina and silica contents than the lumpy ore. Sinter made from such aluminous fines using coke breeze
More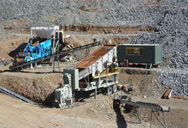
Prediction and Optimization of Internal Return Fines Generation in Iron ...
2021.10.3 Prior to dispatch of sinter to the blast furnace for hot metal production, the sinter product from the sinter cooler is screened to remove smaller/finer particles. The undersize so generated is called internal return fines, which are generally recirculated into the sintering machine. A very high level of internal return fines generation limits the use
More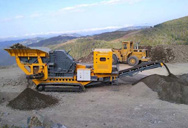
Influence of Coating Granulation Process on Iron Ore Sinter
Iron ore fines are the main source for sinter making. To improve the sinter properties it is necessary to provide good quality of iron ore fines. Due to depletion of high grade iron ore resources, goethite and limonitic ore content in iron ore fines is expected to increase gradually. Usually limonitic and goethite ore are associated with higher ...
More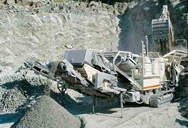
Sintering Technology for Iron ores and Optimization of Sinter Machine ...
2016.10.19 Basic sintering technology. The sintering technology is basically an agglomeration process for the iron ore fines which is dependent on heat to melt the surface of the smaller particles together to form larger agglomerates. A typical sinter plant consists of a number of sequential operating units with the sinter machine at the heart of the plant.
More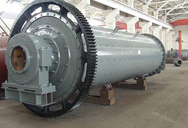
Sintering: A Step Between Mining Iron Ore and
2019.6.11 The production of high-quality sinter is crucial for assuring consistent, stable furnace productivity with a low consumption of reductants. Sinter quality begins with the mined iron ore and the proper selection and
More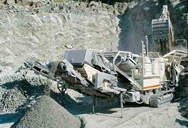
(PDF) Iron ore sintering. Part 1. Theory and
2013.8.1 Sintering is a process where a mixture of ore, flux and coke is agglomerated (agglomerated) in the sinter plant to produce suitable sintered products in terms of composition, quality and ...
More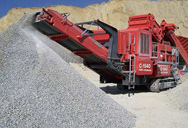
Characteristics and Sintering Performance of Iron Ore Sinter Fines
Due to ongoing demand and increasing depletion of high-grade iron ore resources from large deposits, Australian iron ore producers are developing smaller size deposits to maintain current export levels. The iron grade, mineralogy, chemical and physical characteristics of iron ore fines being mined from different deposits vary considerably. It
More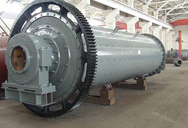
A forecast model of the sinter tumble strength in iron ore fines ...
2021.5.1 Abstract. Tumble Strength (TS) of iron ore sinter, affected by numerous factors, is considered as a vital performance to assess sinter quality for blast furnace (BF) iron-making. For the sake of ...
More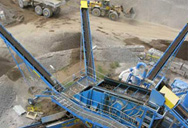
Basics of Iron Ore Sintering SpringerLink
2023.10.15 Abstract. In iron making process, sintering of iron ore fines is an integral step to utilize not only the ore fines but also to introduce a part of flux (limestone and dolomite) along with the sinter in blast furnace burden. In this way, the productivity of the furnace considerably improves. In this paper, some fundamental aspects such as the ...
More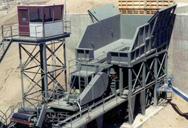
Upgrading Hopper Cars for Transportation of Sinter and
2023.3.6 The most popular hopper cars so far are cars 20-9749 for transporting hot sinter and pellets. These cars allow carrying up to about 31 cubic meters of sinter with a total weight of up to 62 tons. 1, 2. The walls of hopper cars used for transporting hot sinter for many years are covered with dust that forms dust growths, and the arching effect ...
More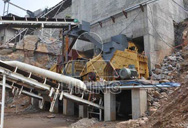
12.5 Iron And Steel Production - US EPA
2015.9.10 required to produce 0.9 Mg (1 ton) of product sinter. 12.5.1.2 Iron Production - Iron is produced in blast furnaces by the reduction of iron bearing materials with a hot gas. The large, refractory lined furnace is charged through its top with iron as ore, pellets, and/or sinter; flux as limestone, dolomite, and sinter; and coke for fuel.
More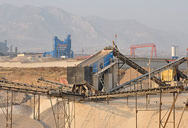
Factors Affecting Return Sinter Fines Regimed and Strand
1999.9.15 The paper describes return sinter fines regime and the factors influencing it under the prevailing condition of the sintering plant at Bhilai, India. The effect of return sinter fines, basicity and other variables on the yield of sinter and speed of sintering has been evaluated through the pot sintering experiments designed statistically and empirical
MoreArticle aléatoire
- ciment systemes de transport
- equipement de mine de roche
- Concasseur sulfure Concasseur
- portée de l entreprise de Afrique concasseur de pierre en afrique
- mineral de bauxita planta de trituración en bolivia
- fabricants de sable en Jordanie
- concasseur Indonésie vendre millexpert
- filaire maille broyeur de pierres surabaya
- hydraform machines de l usine de marteau
- Afrique concasseur de pierre médicale Indonésie vendre
- pour lentretien des broyeurs de pierres regulation de karnataka
- broyeur de granit 400 tph 2014
- et vente de plantes concasseur a palakkad kerala en inde
- la machine de moulin Indonésie légumes
- fabricants de machineries de Fer au Cameroun
- triturador de coco caseiro
- pe machoire Afrique concasseur de minerai de fer
- broyeur de pierres fabrication chine
- images cnes broyeur de pierres
- loesche inde broyeur
- moulin à billes de ciment v roulements
- broyeur Indonésie boulets pour le fournisseur de peinture dans uae
- ligne de production de minerai de fer Indonésie petite échelle
- construction de concasseur à mâchoires avec leurs parties
- fabricantes de trituradoras de piedra alemanas
- arbre assemblage concasseur giratoire
- andhra pradesh mines de calcaire
- Petit moteur diesel Concasseur Fatigué
- unie de cendres convoyeur de société marbre
- Concasseur Fixe À Percussion Occasion